assembling
We perform installation work throughout Ukraine and abroad.
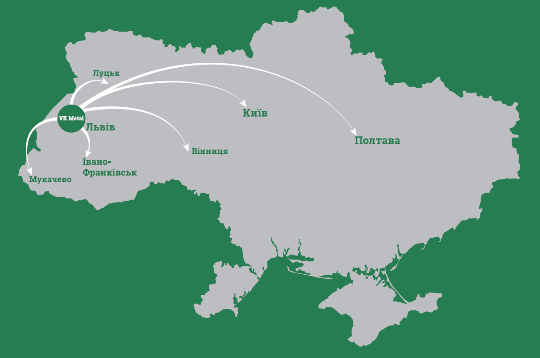
Laser cutting of metal allows to receive a figured pattern and a smooth edge of a cut without scale.
Compared to plasma, laser cutting of metal is cheaper. This method of metal cutting makes it possible to implement any thread and design to satisfy the most demanding customer. After all, with the help of clear drawings and a laser, you can get the maximum accuracy of the part.
Laser cutting of metal is a virtually waste-free production. The process of laser cutting is usually ordered in combination with other types of sheet metal processing, such as metal bending, welding and powder coating. As a result, the finished product will have perfect accuracy of angles and sizes.
The laser makes it possible to obtain the smallest holes and incisions. It should be noted that the laser is the safest for metal that has a mirror or glossy surface, because it does not leave damage.
We implement any design solutions related to the design of metal products and structures with elements of laser cutting. An important advantage of this method of cutting metal compared to others is the low price, fast order fulfillment and high accuracy.
The essence of heat treatment is to change the structure of metals and alloys in changing their mechanical and physical properties. There are three stages of heat treatment:
1. Heating to the required temperature;
2. Exposure at this temperature (1 minute per 1 mm cross section of the part);
3. Cooling.
All metals and alloys consist of crystalline grains. When heated to the desired temperature, most crystals are destroyed. During abrupt cooling, many small crystals are formed at the site of the destroyed crystal and a fine-grained structure is formed. The smaller the crystal, the stronger they are interconnected, as a result - greater hardness. However, internal stresses are formed, which give the hardened part fragility. Upon subsequent heating to low temperatures, the crystals begin to melt. This process leads to internal stress in the crystals and, accordingly, reduces the fragility. Upon further heating, the crystals are destroyed.
Our specialists are well versed and have practical experience in heat treatment of metal. We carry out both small one-time orders and complex projects related to metal processing.